How to improve the processing accuracy of CNC milling machines?
7 min read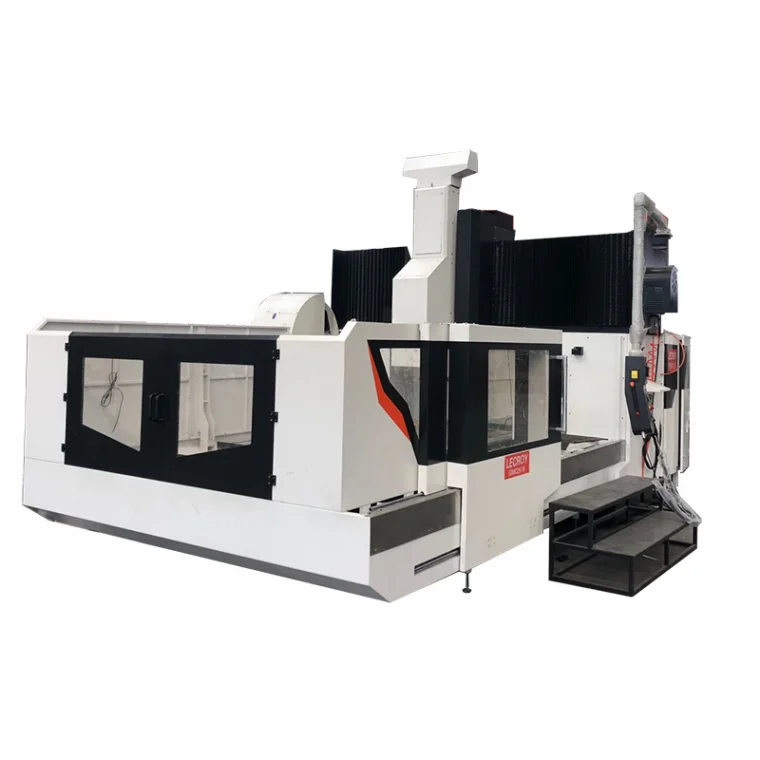
With the continuous development of the manufacturing industry, especially the increasing demand for high-precision parts and complex-shaped parts, CNC milling machines, as modern processing equipment, have become one of the core equipment in many industries due to their excellent processing accuracy and automation level. CNC milling machines can perform precision cutting in multiple axes through the control of computer numerical control systems, thereby improving production efficiency and part accuracy. However, in actual production, how to improve the processing accuracy of CNC milling machines is still a matter of great concern.
This article will explore the ways to improve the processing accuracy of CNC milling machines from multiple aspects, including the improvement of the accuracy of the equipment itself, programming optimization, tool selection, and maintenance, reasonable setting of cutting parameters, environmental control, and other factors.
1. Improvement of the accuracy of CNC milling machine equipment
The processing accuracy of CNC milling machines is directly affected by the hardware of the equipment. Therefore, improving the accuracy of the CNC milling machine itself is the first step to ensure processing accuracy. The following are several key aspects:
Rigidity of machine tools: Machine tool rigidity is the basis for CNC milling machines to improve processing accuracy. Machine tools with good rigidity can effectively suppress vibration and avoid deformation during cutting. The rigidity of CNC milling machines is usually closely related to the design, material selection, and structural stability of the machine tools. High-rigidity machine tools can provide a more stable cutting process and reduce machining errors caused by vibration, thermal expansion, or external forces.
Precision guides and lead screws: Guides and lead screws are crucial components in CNC milling machines, responsible for ensuring the precise positioning and movement of the machine tool. The use of high-precision ball screws and high-rigidity linear guides can effectively improve the positioning accuracy and repeatability of the machine tool. Regularly check and lubricate these components to avoid precision deviations caused by wear or improper lubrication.
Stability of the CNC system: As the brain of the CNC milling machine, the control accuracy and response speed of the CNC system directly affect the machining accuracy. The selection of high-quality and stable CNC systems is an important part of improving machining accuracy. Optimization of CNC system parameter settings, signal processing, feedback loops, etc. can significantly improve machining accuracy.
Thermal deformation control: During high-speed and high-load machining, the components of the CNC milling machine (especially the spindle and worktable) will expand thermally due to the heat generated by cutting, thereby affecting the machining accuracy. By using an efficient cooling system and controlling the ambient temperature of the machine tool, the impact of thermal expansion on machining accuracy can be effectively reduced. For example, the spindle of a CNC milling machine can be equipped with a liquid cooling system to help control temperature rise and reduce the interference of temperature fluctuations on machining accuracy.
2. Optimize CNC programming
CNC programming is one of the important factors affecting machining accuracy. Optimizing programming can not only improve machining efficiency but also effectively control errors during machining. The following are some methods for optimizing programming:
Reasonably select cutting paths: When programming, rationally planning the cutting path of the tool can reduce the tool's movement distance, avoid unnecessary empty running, and reduce vibration and error generation. For example, using the shortest path cutting scheme to avoid long-term empty running can reduce machining errors caused by vibration or uneven cutting force.
Optimize tool compensation: Tool compensation is a key link in CNC programming, which can adjust the machining path according to tool wear. Through accurate tool compensation, it can ensure that the tool position during machining is consistent with the preset path, thereby ensuring machining accuracy.
Choose the appropriate machining sequence: The choice of machining sequence also has an important impact on machining accuracy. In multi-process machining, rationally arranging the machining sequence can avoid unnecessary tool replacement, workpiece clamping changes, and other factors, and reduce error accumulation. Usually, rough machining is performed first, and then fine machining is performed to ensure the overall accuracy of the workpiece.
Use high-precision virtual simulation: Modern CNC systems are usually equipped with virtual simulation functions, which can simulate the machining process before actual machining. Through virtual simulation, it is possible to check whether there are problems such as collision and interference in the tool path, so as to optimize the machining plan and ensure machining accuracy.
3. Tool selection and maintenance
The selection and maintenance of tools directly affect the machining accuracy of CNC milling machines. Factors such as the quality, material, and geometry of the tool will affect the cutting force, cutting heat, etc. during the cutting process, and thus affect the machining accuracy of the workpiece.
Select suitable tool materials: Tool materials should be selected according to the characteristics of the workpiece material. Tool materials such as cemented carbide, ceramics, and cubic boron nitride (CBN) have better performance when machining materials with higher hardness. By selecting suitable tool materials, the cutting performance can be improved, the wear and deformation during the cutting process can be reduced, and the machining accuracy can be improved.
Optimization of tool geometry: The geometry of the tool, such as the rake angle, back angle, and tip angle of the tool, will also affect the mechanical properties during the cutting process. Reasonable tool geometry can effectively reduce factors such as cutting force and vibration and improve machining accuracy.
Regular inspection and replacement of tools: Tool wear will lead to uneven distribution of cutting force, which will affect the processing accuracy. Regular inspection of tool wear and replacement of tools at appropriate times can ensure processing accuracy. Modern CNC milling machines are usually equipped with tool wear monitoring systems, which can monitor tool status in real-time, adjust processing parameters or replace tools in time.
4. Reasonable setting of cutting parameters
The setting of cutting parameters directly determines the stability and processing accuracy of the cutting process. Reasonable cutting parameters can reduce vibration, deformation, tool wear, etc. during the cutting process and improve processing accuracy.
Selection of cutting speed and feed rate: Cutting speed and feed rate are important parameters affecting processing accuracy. Excessive cutting speed and feed rate will lead to excessive cutting force and vibration, which will affect processing accuracy. Conversely, too low a cutting speed or too small a feed rate may lead to low processing efficiency and increased processing time. According to different materials and processing requirements, selecting the appropriate cutting speed and feed rate can ensure the balance of processing accuracy and efficiency.
Optimization of cutting depth: Cutting depth is another important factor affecting processing accuracy. A larger cutting depth may lead to uneven distribution of cutting force, thereby affecting the surface accuracy of the workpiece. Generally speaking, the cutting depth can be appropriately increased during rough machining, while the cutting depth should be appropriately reduced during fine machining to ensure machining accuracy.
Use appropriate cutting fluid: Cutting fluid can not only effectively reduce cutting temperature, but also reduce the friction between the tool and the workpiece, thereby improving machining accuracy. Selecting a suitable cutting fluid and ensuring that its flow rate and spraying angle are appropriate can effectively reduce the thermal expansion and deformation generated during the cutting process and improve machining accuracy.
5. Environmental control and error compensation
The machining accuracy of CNC milling machines is also affected by environmental factors. During the machining process, factors such as temperature, humidity, and vibration may affect the accuracy. Therefore, taking effective environmental control measures is also an important means to improve machining accuracy.
Temperature control: Since the machine tool generates heat during operation, temperature fluctuations will cause thermal expansion of various parts of the machine tool, thereby affecting the machining accuracy. To reduce the impact of temperature changes, the workshop temperature can be controlled by an air conditioning system or a constant temperature device to ensure that the machine tool operates in a stable temperature environment.
Prevent vibration interference: Vibration is a major factor affecting machining accuracy. During the machining process, any external vibration or vibration of the machine tool itself may cause workpiece machining errors. By selecting a suitable machine tool foundation, installing a shock-absorbing device, and optimizing cutting parameters, the impact of vibration on machining accuracy can be reduced.
Error compensation technology: Modern CNC systems generally use error compensation technology to improve machining accuracy by performing real-time compensation for thermal deformation, geometric errors, servo errors, etc. of machine tools. Error compensation technology can automatically adjust the motion trajectory of machine tools to compensate for the accuracy deviation caused by mechanical errors or environmental changes, thereby significantly improving machining accuracy. This compensation technology usually includes thermal compensation, geometric error compensation, axial error compensation, etc., and the error is measured and corrected in real-time through the CNC system to ensure that the final machining result meets the predetermined accuracy requirements.
In short, improving the machining accuracy of CNC milling machines is a systematic project that needs to be started from multiple aspects. Through all-round optimization and management, the machining accuracy of CNC milling machines can reach an extremely high level, providing more reliable machining solutions for high-end manufacturing fields such as aviation, automobiles, mold manufacturing, and precision medical devices. It is hoped that the methods and suggestions provided in this article can help engineers and technicians achieve better results in actual work.
www.bofengmachinery.com
bofengmachinery