Transmission Performance of Slew Drive for Solar Tracker
5 min read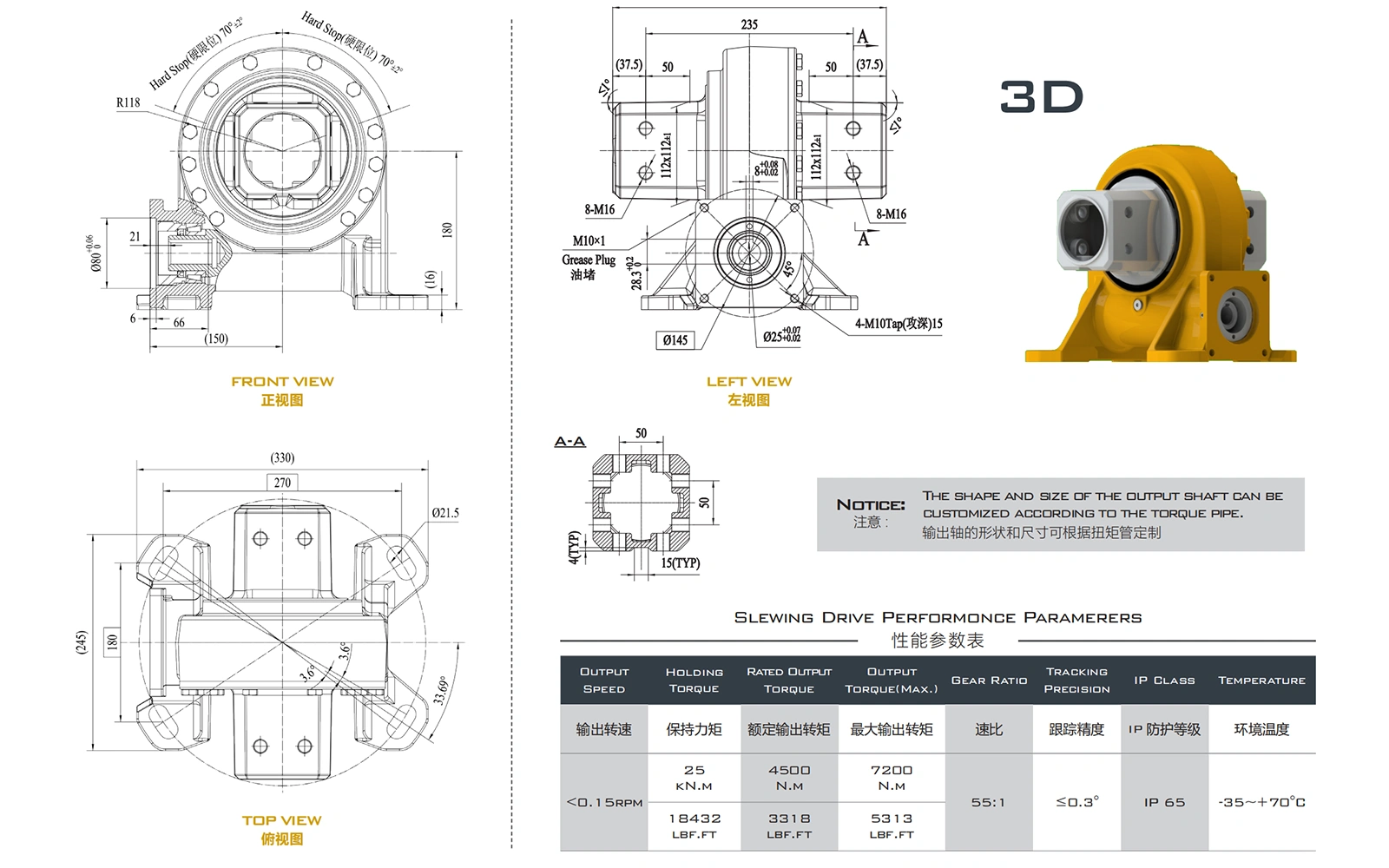
In the renewable energy landscape, solar tracking systems have become critical in maximizing the efficiency of photovoltaic (PV) modules by orienting them toward the sun' s position throughout the day. A pivotal component in single-axis and dual-axis solar trackers is the *slew drive*, a compact rotational drive that combines gears, bearings, and housing in a self-contained system. The transmission performance of a slew drive is paramount in ensuring accurate solar tracking, structural stability, and long-term durability. In this blog post, as a high quality slewing drive manufacturer, YOJU will share the transmission performance of slew drive for solar tracker, including mechanical design, gear transmission efficiency, etc.
1. Slew Drive for Solar Tracker Mechanical Design
A slew drive is essentially a gearbox that facilitates rotational movement along an axis. In solar tracking applications, it is responsible for positioning solar panels to follow the sun's trajectory either along a single axis (azimuth or elevation) or along dual axes (azimuth and tilt).
Unlike traditional rotary actuators, slew drives integrate a worm gear mechanism with a slewing bearing. This design enables high torque transmission in a compact footprint, making it ideal for solar tracker systems that demand precision, load-holding capability, and minimal maintenance.
2. Key Parameters Influencing Transmission Performance
Transmission performance in slew drives can be evaluated based on several mechanical and operational parameters. These include:
* Gear Ratio
* Transmission Efficiency
* Torque Output
* Backlash and Positioning Accuracy
* Load-Carrying Capacity
* Durability and Wear
* Sealing and Environmental Resistance
Each of these parameters contributes to how effectively and efficiently the slew drive converts motor input into accurate, controlled movement.
3. Gear Ratio and Its Impact on Performance
The gear ratio of a slew drive directly affects both the torque output and the rotational speed of the drive. Most solar tracking applications require a high reduction ratio (often between 30:1 and 150:1), which allows a small input torque from a motor to be amplified significantly.
A higher gear ratio generally improves the load-holding capacity and self-locking behavior, which is crucial for maintaining position under wind or snow loads. However, it also reduces the speed of actuation, which is acceptable in solar applications since tracking adjustments are relatively slow and infrequent.
4. Transmission Efficiency and Energy Consumption
Efficiency in a slew drive is primarily dictated by the type of gear system employed—typically a worm gear in solar trackers. Worm gears inherently have lower mechanical efficiency, ranging between 30% and 70%, due to sliding contact between the worm and the gear teeth.
To optimize efficiency:
* The worm and gear material combination (e.g., hardened steel and bronze) should be carefully selected for low friction and wear.
* Surface treatments and lubricants can significantly reduce energy losses due to friction.
* Helical worm gears or double enveloping worm designs may be used to enhance contact surface area and reduce slip.
In solar tracking systems powered by electric motors and photovoltaic energy, transmission efficiency becomes a direct contributor to net energy yield, making it a critical design factor.
5. Torque Transmission and Load Handling
The torque capacity of a slew drive is a core performance metric. Solar trackers must endure dynamic and static loads caused by wind, snow, and seismic activity, in addition to the weight of the PV modules themselves.
Torque performance is influenced by:
* Module mounting configuration (central or offset load)
* Bearing size and type (four-point contact bearings or crossed roller bearings)
* Gear material strength
* Input torque from the actuator or motor
Peak torque ratings must be established for both dynamic (operational) and static (holding) conditions. Most commercial slew drives for solar trackers are rated in the range of 500 Nm to 100,000 Nm, depending on application scale.
6. Backlash and Positioning Accuracy
Backlash, or the small gap between gear teeth during direction reversal, can significantly impact the positioning accuracy of a solar tracker. Excessive backlash leads to poor tracking precision and reduced solar collection efficiency.
To mitigate backlash:
* Precision-machined worm and gear sets are used.
* Preloaded bearings can eliminate axial and radial play.
* Backlash compensation mechanisms or dual-worm systems (with counter-rotation) may be employed.
* High-tolerance manufacturing and alignment during assembly reduce inconsistencies.
For solar applications, a positioning accuracy within ±0.1° is generally acceptable. Achieving this level of accuracy requires balancing backlash reduction with mechanical cost and complexity.
7. Durability, Wear, and Maintenance
Slew drives must perform reliably over the 20–30 year lifespan typical of solar installations. Mechanical wear due to continuous meshing of gears, combined with environmental factors such as temperature cycling, dust, and humidity, can degrade performance.
Key approaches to enhancing durability include:
* Use of heat-treated gear components to increase surface hardness.
* Enclosed housings with high IP (Ingress Protection) ratings to prevent contamination.
* Periodic lubrication systems, or sealed-for-life bearings and gears.
* Corrosion-resistant materials, especially for outdoor applications in coastal or desert environments.
Monitoring systems that track torque load, angular position, and internal temperature can also be integrated to anticipate wear and enable predictive maintenance.
8. Environmental Adaptability
Solar trackers are deployed in a wide range of environments—from arid deserts to icy plateaus. The slew drive must withstand these conditions without performance degradation.
Important environmental design considerations include:
* Sealing and Ingress Protection: IP66-rated casings protect against water jets and dust ingress.
* Temperature Range: Materials and lubricants must function reliably between –40°C and +60°C.
* UV and Corrosion Resistance: Paint coatings and anodized finishes protect against UV radiation and oxidation.
Additionally, the use of temperature-compensating materials and composite bushings can help maintain structural integrity across temperature swings.
9. Integration with Control Systems
Modern slew drives are increasingly integrated with sensor feedback and motor controllers to enable closed-loop positioning. This allows for:
* Real-time adjustment of tracking angles
* Fault detection (e.g., over-torque or misalignment)
* Synchronization across multiple trackers in large PV farms
Electromechanical slew drives often use DC motors with encoders or stepper motors, offering digital control precision. Integration with SCADA (Supervisory Control and Data Acquisition) systems enables large-scale coordination and remote monitoring.
10. Design Trade-offs and Optimization
Designing a slew drive involves trade-offs between:
* Torque vs. Speed (gear ratio selection)
* Efficiency vs. Self-locking capability (especially in worm gears)
* Cost vs. Durability (material and manufacturing quality)
* Complexity vs. Maintainability (sealed vs. serviceable designs)
For solar tracking systems, the optimal solution usually leans toward high torque, self-locking, and maintenance-free operation over decades. The upfront investment in a high-quality slew drive pays off in reduced downtime, lower operating costs, and increased energy harvest.
Conclusion
The transmission performance of slew drives directly influences the efficiency, reliability, and lifespan of solar tracking systems. Engineers and system designers must evaluate gear ratios, torque capacity, efficiency, backlash, and environmental sealing when selecting or designing a slew drive. As solar energy continues to expand globally, innovations in slew drive technology—including smart monitoring, advanced materials, and improved gearing mechanisms—will play a critical role in pushing the boundaries of renewable energy efficiency.
Understanding the nuanced interplay of mechanical and environmental factors ensures optimal design and deployment of slew drives, making them an indispensable component in the pursuit of sustainable, high-performance solar energy systems.
www.enyoju.com
YOJU