Why Alumina Catalyst Supports Are Crucial for Modern Industrial Catalysis
4 min read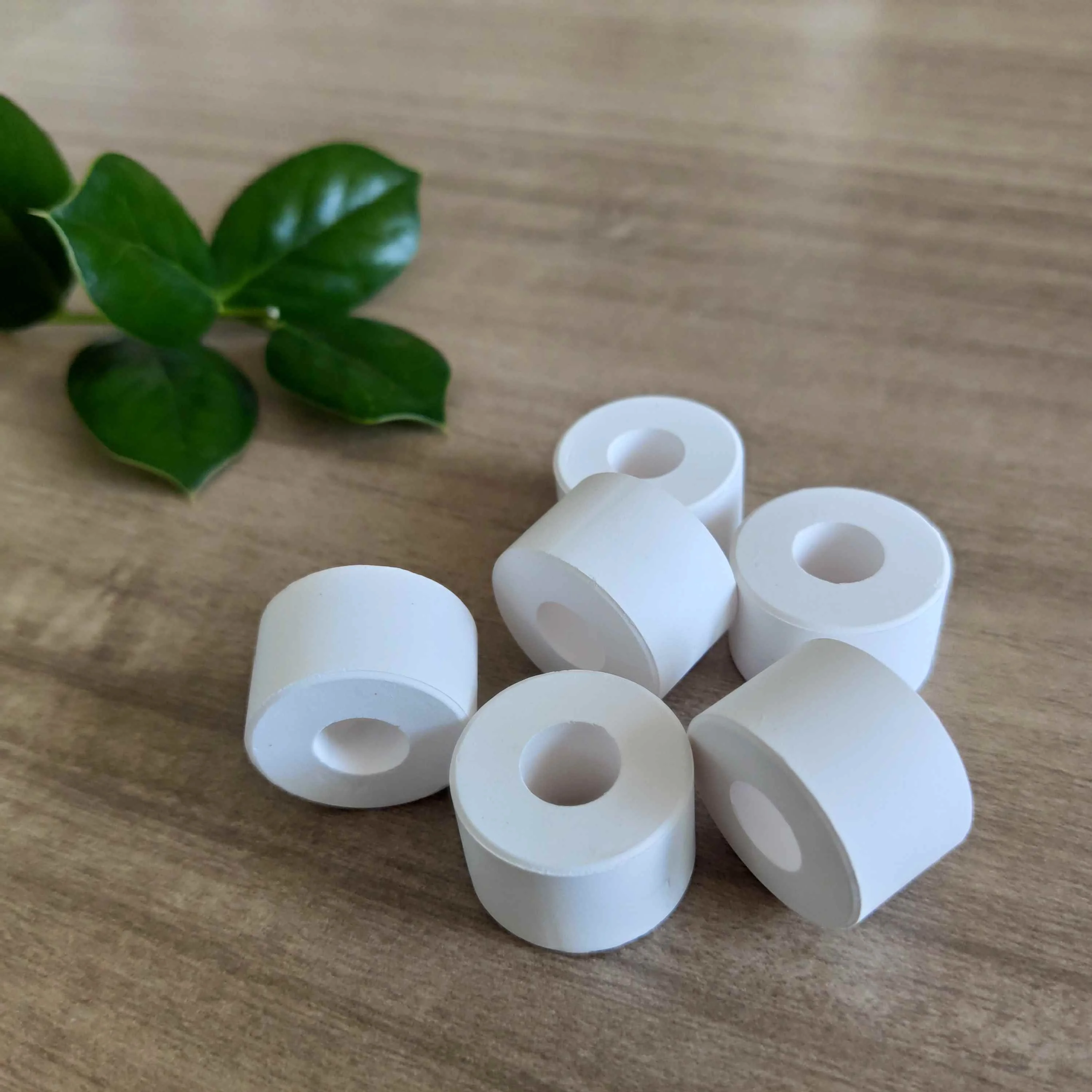
In the world of industrial chemistry, catalysis is the backbone of countless essential processes — from refining crude oil to manufacturing fertilizers and environmental remediation. Yet, while active catalysts like metals or enzymes get most of the spotlight, the unsung hero that ensures their efficiency, longevity, and stability is often the catalyst support. Among these support materials, alumina (Al₂O₃) stands out as one of the most versatile and indispensable options.
In this blog, we’ll dive deep into why alumina catalyst supports are critical for modern industrial catalysis, what makes them unique, and how they are driving innovation in industries around the world.
What is a Catalyst Support?
Before understanding alumina’s role, it's important to know what a catalyst support does. A catalyst support is a solid material used to disperse and stabilize the active catalytic component, usually metals like platinum, palladium, nickel, or cobalt. The support provides a high-surface-area structure that ensures maximum exposure of the active material to reactants, which is essential for efficient catalytic reactions.
Supports also influence:
Thermal and mechanical stability
Dispersion of active components
Resistance to sintering or deactivation
Control over reaction pathways
Alumina: The Gold Standard in Catalyst Supports
Alumina (Al₂O₃) is one of the most widely used catalyst supports in industrial applications — and for good reasons. It offers a unique combination of thermal stability, high surface area, mechanical strength, and tunable porosity, making it suitable for a broad range of chemical processes.
Some common forms of alumina used as catalyst supports include:
Gamma-alumina (γ-Al₂O₃): High surface area and commonly used in hydroprocessing and petrochemical reactions.
Alpha-alumina (α-Al₂O₃): Very stable at high temperatures, but lower surface area.
Eta, Theta, and Delta phases: Intermediate forms with varying properties for specialized applications.
Key Properties that Make Alumina Ideal
1. High Surface Area
Catalytic reactions occur on the surface of the active material, so a higher surface area leads to more available reaction sites. Gamma-alumina typically has a surface area ranging from 100 to 300 m²/g, providing ample room for the dispersion of active metal nanoparticles. This makes it ideal for processes requiring high catalytic efficiency, such as hydrogenation and oxidation reactions.
2. Thermal and Chemical Stability
Industrial catalytic processes often take place under extreme conditions — high temperatures, pressures, and aggressive chemical environments. Alumina excels in these scenarios:
Stable up to ~1000°C, depending on the phase
Inert to many chemical species
Resistance to phase transformation and sintering
This makes alumina the go-to support in hydrotreating, catalytic cracking, and reforming reactions.
3. Mechanical Strength
In fixed-bed reactors and fluidized catalytic systems, the physical durability of the support material is essential. Alumina’s mechanical hardness and abrasion resistance help maintain catalyst integrity during extended operation, especially in dynamic systems like fluid catalytic cracking (FCC).
4. Tunability and Porosity
Alumina can be engineered with specific pore sizes and distributions, enabling the design of catalysts that match the size and diffusion properties of target molecules. This tailored porosity is crucial in:
Selective catalytic reduction (SCR)
Methanol-to-olefins (MTO)
Ammonia synthesis and decomposition
Alumina Supports in Key Industrial Applications
Petrochemical and Refining
Alumina-supported catalysts are central to the petrochemical industry, particularly in:
Hydrotreating: Removal of sulfur, nitrogen, and aromatics from fuels using NiMo or CoMo on alumina.
Hydrocracking: Alumina supports platinum or palladium in converting heavy hydrocarbons into lighter fractions.
Catalytic reforming: Where Pt/alumina catalysts are used to improve fuel octane rating.
Environmental Catalysis
Environmental applications of alumina-supported catalysts include:
Vehicle emission control: Three-way catalysts (TWC) use alumina to disperse noble metals (Pt, Rh, Pd) that reduce NOx, CO, and hydrocarbons.
VOC abatement: Alumina-supported metal oxides oxidize volatile organic compounds in exhaust streams.
DeNOx systems: Vanadium or copper on alumina is employed for selective catalytic reduction (SCR) of NOx emissions in power plants.
Chemical Synthesis
In the field of fine chemicals and pharmaceuticals, alumina-supported catalysts provide high activity and selectivity in reactions such as:
Hydrogenation
Dehydration
Oxidation
Dehydrogenation
Its versatility enables tailored formulations for batch and continuous flow synthesis environments.
Alumina as a Functional Material Beyond Support
Interestingly, alumina isn't just a passive support. It can participate actively in some reactions or affect catalyst behavior by modifying:Acid-base properties of the catalyst
Reaction intermediates through surface interaction
Coke formation and deactivation rates
For example, in dehydration reactions, alumina’s Lewis acid sites play an active catalytic role, making it useful in converting alcohols to olefins.
Conclusion
Alumina catalyst supports are an essential component of modern industrial catalysis. Their outstanding thermal stability, high surface area, tunable porosity, and mechanical strength make them suitable for a wide variety of demanding applications across the chemical, petrochemical, and environmental sectors.
As process demands become more complex and performance expectations rise, engineered alumina supports will continue to evolve, offering tailored solutions for the next generation of catalytic technologies.
Yixing Winner Technology Co., Ltd. is a professional manufacturer in producing catalysts and their ceramic carriers, ceramic glove formers, and other industrial ceramics.
Welcome to inquiry if you need to know more about alumina catalyst supports details or order wholesale.
E-mail:camilleyxwn@outlook.com
www.yxwntec.com
Yixing Winner Technology Co., Ltd.