Dual-Axis U-Type Welding Positioner: A Precision Positioning Solution in Welding Processes
5 min read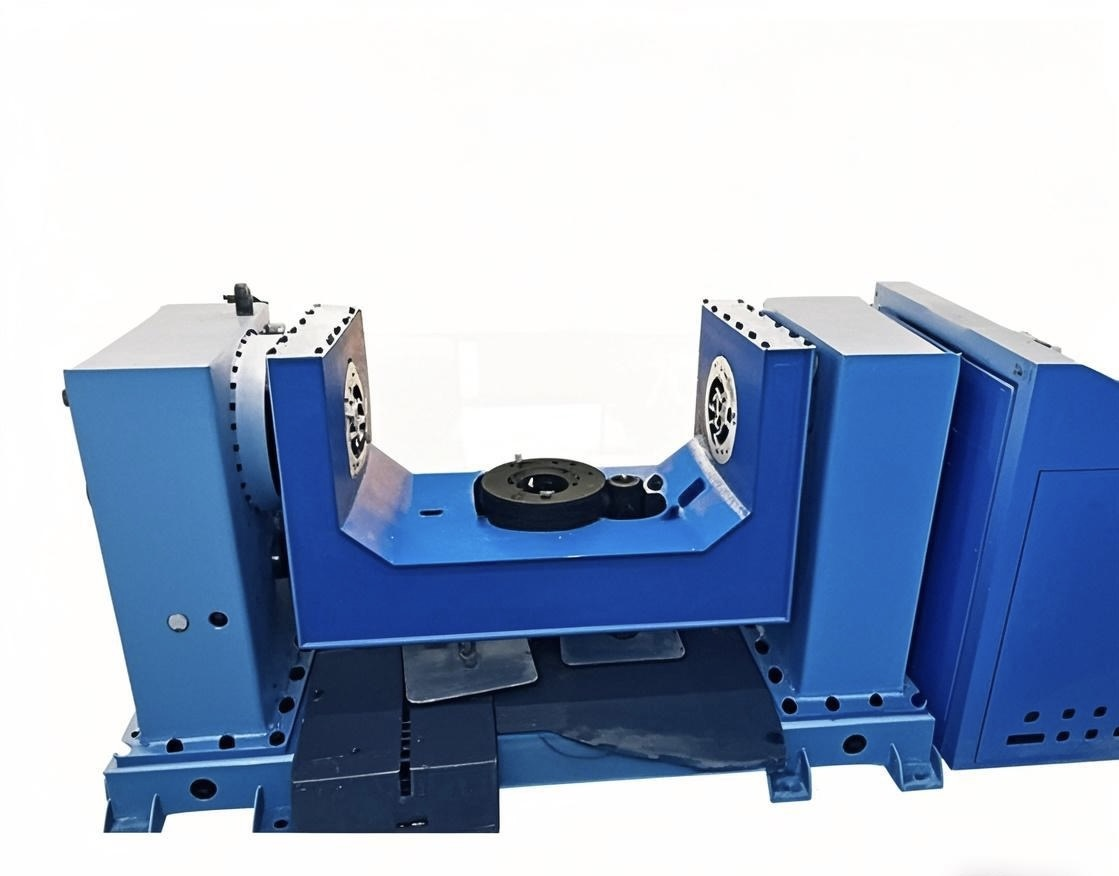
In the field of welding, the dual-axis U-type welding positioner has become an indispensable core tool in modern welding processes due to its high precision and multifunctional capabilities. Whether for manual welding or automated robotic welding, the dual-axis U-type welding positioner significantly enhances welding efficiency and quality with its unique design and features. Compared to traditional single-axis positioners or ordinary rotary tables, the dual-axis U-type welding positioner offers distinct advantages in flexibility, precision, and adaptability, making it ideal for complex welding tasks.
Core Features of the Dual-Axis U-Type Welding Positioner
The design philosophy of the dual-axis U-type welding positioner revolves around "precision positioning" and "multifunctional operation." Its core features include:
1. Dual-Axis Motion Control
The dual-axis U-type welding positioner is equipped with two independent motion axes: a rotation axis and a tilt axis. The rotation axis handles the horizontal rotation of the workpiece, while the tilt axis enables vertical tilting. This dual-axis design allows the workpiece to be freely adjusted in three-dimensional space, ensuring the weld seam is always in the optimal position during welding.
2. U-Type Frame Structure
Unlike traditional C-type or H-type frames, the U-type frame provides a larger operating space and greater load-bearing capacity. Its open design facilitates easy loading and unloading of workpieces while accommodating various shapes and sizes.
3. High-Precision Drive System
The dual-axis U-type welding positioner utilizes high-performance servo motors and precision reducers to achieve accurate control of rotation and tilting speeds. Its motion precision typically reaches ±0.1°, meeting the demands of high-precision welding tasks.
4. Modular Design
Modern dual-axis U-type welding positioners often feature a modular design, allowing users to customize fixtures, control systems, and additional functions such as automatic centering and laser positioning.
Technical Advantages of the Dual-Axis U-Type Welding Positioner
1. Improved Welding Efficiency
By automating workpiece positioning, the dual-axis U-type welding positioner reduces operator time and physical effort. For example, when welding large structural components, traditional methods may require multiple manual adjustments, whereas the dual-axis positioner can quickly achieve the desired position through control system inputs.
2. Enhanced Welding Quality
Precise control of rotation and tilting angles ensures the weld seam remains in flat or horizontal positions, minimizing defects such as porosity and slag inclusion. Additionally, its stable motion performance effectively prevents vibration and deviation during welding.
3. Adaptability to Complex Workpieces
The dual-axis U-type welding positioner is particularly suitable for welding complex structures, such as irregular pipes, polyhedral frames, and large containers. Its U-type frame and dual-axis motion design easily accommodate multi-angle welding requirements.
4. Compatibility with Automated Welding
In robotic welding systems, the dual-axis U-type welding positioner seamlessly integrates with welding robots to achieve automatic workpiece positioning and welding. This combination not only improves production efficiency but also reduces human error.
Applications of the Dual-Axis U-Type Welding Positioner
1. Pressure Vessel Manufacturing
In pressure vessel welding, the dual-axis U-type welding positioner is used to rotate and tilt cylindrical bodies, ensuring the quality of circumferential and longitudinal welds. Its high-precision motion control meets the stringent requirements for weld sealing and strength.
2. Wind Power Equipment Welding
The welding of wind turbine towers and blades requires highly stable and precise positioning equipment. The dual-axis U-type welding positioner, with its robust load capacity and precise motion control, is an ideal choice for wind power equipment manufacturing.
3. Aerospace Component Welding
The aerospace industry demands exceptionally high welding quality. The dual-axis U-type welding positioner meets the high-precision welding needs of complex structures, such as engine casings and fuel tanks.
4. Automotive Component Welding
In automotive manufacturing, the dual-axis U-type welding positioner is used for welding chassis, frames, and exhaust systems. Its efficiency and flexibility align with the high-volume production requirements of the automotive industry.
Differences Between Dual-Axis U-Type Welding Positioners and Traditional Positioners
1. Degrees of Freedom
Traditional single-axis positioners only allow for single-axis rotation or tilting, while dual-axis U-type welding positioners provide higher degrees of freedom through dual-axis motion control, meeting the multi-angle welding needs of complex workpieces.
2. Load Capacity
The U-type frame design of dual-axis welding positioners offers greater load capacity, making them suitable for large and heavy workpieces.
3. Precision Control
Dual-axis U-type welding positioners use high-precision servo motors and reducers, offering superior motion accuracy compared to traditional positioners, which is essential for high-precision welding tasks.
4. Intelligent Features
Modern dual-axis U-type welding positioners are equipped with intelligent control systems, supporting parameterized programming, automatic centering, and remote control, whereas traditional positioners often rely on manual operation.
Selection and Configuration of Dual-Axis U-Type Welding Positioners
1. Based on Workpiece Size
When selecting a dual-axis U-type welding positioner, consider the size, weight, and shape of the workpiece. For large workpieces, choose models with higher load capacity and larger operating space.
2. Based on Welding Process
Different welding processes have varying requirements for motion precision and speed. For example, laser welding demands higher precision, while arc welding requires more stable motion performance.
3. Automation Requirements
If integrating the positioner with a welding robot, opt for models that support full automation and communication interfaces.
4. Additional Functions
Depending on specific needs, users can select additional features such as automatic centering, laser positioning, and collision protection to enhance performance and safety.
Maintenance and Care for Dual-Axis U-Type Welding Positioners
1. Regular Lubrication
Regularly lubricate the rotation and tilt axes to reduce wear and extend the equipment's lifespan.
2. Electrical System Inspection
Periodically check the motors, reducers, and control systems to identify and resolve potential issues.
3. Equipment Cleaning
Keep the positioner clean to prevent dust and debris from affecting its operation.
4. Regular Calibration
For high-precision welding tasks, regularly calibrate the positioner's motion accuracy to ensure optimal performance.
Conclusion
The dual-axis U-type welding positioner, with its unique design and exceptional performance, has become an indispensable tool in modern welding processes. Its dual-axis motion control, high-precision drive system, and modular design make it far superior to traditional positioners in terms of flexibility, precision, and adaptability. Whether for pressure vessels, wind power equipment, or aerospace components, the dual-axis U-type welding positioner significantly enhances welding efficiency and quality.
For companies looking to upgrade their welding processes, investing in a high-performance dual-axis U-type welding positioner is a wise decision. Through proper selection, correct usage, and regular maintenance, the dual-axis U-type welding positioner will become an essential precision positioning solution in welding production.
www.resizeglobal.com
Wuxi Yuanpeng Machinery