Optimizing Injection Molding with High-Performance Mold Bases
4 min read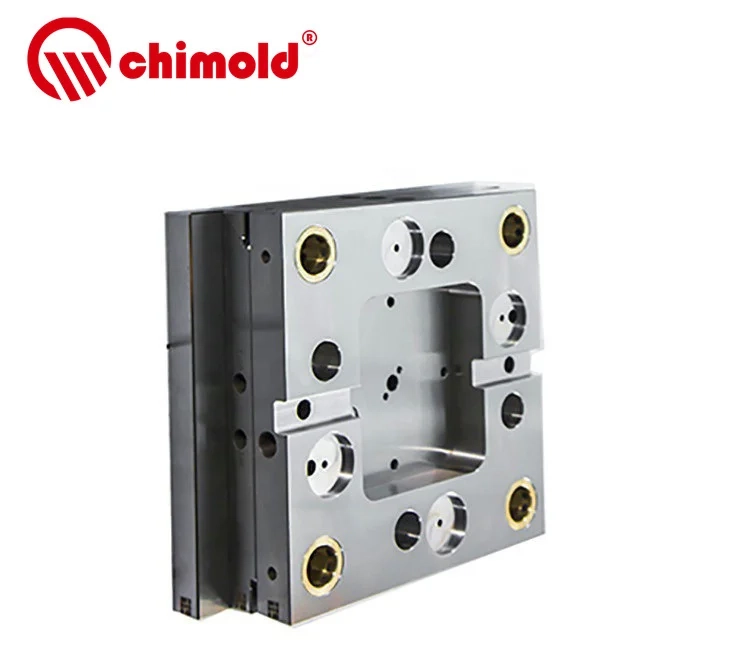
A mold base is a foundational component in the injection molding process, serving as a crucial framework that holds the mold cavity, core inserts, cooling systems, and ejection mechanisms in place. It plays an integral role in shaping, cooling, and ejecting molded parts with high precision. Its structural and functional characteristics can significantly influence the quality, productivity, and cost-effectiveness of manufacturing operations. In this article, Chimold delves into the importance of mold bases and how they contribute to injection molding product quality.
The Importance of Mold Base in Injection Molding
The mold base is essential for the injection molding process as it provides the structural integrity and stability needed to keep the mold cavity and core properly aligned. It is responsible for holding the various components of the mold together, ensuring that the plastic parts being molded maintain tight tolerances and consistent quality. The mold base also houses critical elements like cooling channels and ejection systems, which help to control temperature and facilitate part removal.
One of the primary functions of the mold base is to regulate thermal management within the mold. Effective cooling is vital for preventing defects such as warping, shrinkage, and residual stresses, which can occur due to uneven cooling rates. The mold base allows the integration of cooling channels that help dissipate heat efficiently and consistently. By maintaining uniform cooling across the mold, the mold base minimizes part distortion and ensures that the molded products meet the desired specifications.
Moreover, the structural stability provided by the mold base reduces the likelihood of misalignment or mold shift during the molding process, which could otherwise lead to defects such as flash, dimensional inaccuracies, or poor surface finish. This makes mold bases not only a physical support structure but a key factor in achieving consistent, high-quality production, even in complex or high-volume molding operations.
How Mold Bases Contribute to Injection Molding Product Quality
Mold bases are fundamental to ensuring the overall quality and efficiency of the injection molding process. Serving as the foundation that supports the mold components, a mold base provides the critical structure and stability necessary for precise and repeatable molding operations. A high-quality mold base ensures that all components are securely positioned, reducing the risk of misalignment, dimensional inaccuracies, or deformation in the molded parts. This stability is particularly important in high-volume production where even minor shifts can lead to significant defects over time.
One of the most significant contributions of mold bases to product quality lies in their ability to maintain the integrity of the mold cavity. The mold cavity is responsible for shaping the injected plastic, and its exact dimensions must be preserved to achieve consistent part geometry. A sturdy mold base helps to maintain the alignment of the mold halves, ensuring that each part produced meets strict dimensional tolerances. This is crucial for industries such as automotive, medical devices, and electronics, where precision is non-negotiable.
Another essential factor is thermal management. During the injection molding process, temperature control is vital for producing high-quality parts. Mold bases are designed to facilitate efficient heat dissipation, allowing the molten plastic to cool and solidify uniformly. Poor thermal regulation can result in a range of defects, such as warping, shrinkage, or uneven surface finishes, which can compromise the functionality or aesthetics of the product. A well-constructed mold base prevents such issues by ensuring that heat is distributed evenly across the mold, contributing to smoother and more consistent cooling cycles.
In addition to thermal control, mold bases play a key role in the ejection process. Once the plastic part has solidified, it must be ejected from the mold without causing damage to its surface or structure. Mold bases are equipped with ejector pins and other mechanisms that assist in this process, ensuring that parts are removed cleanly and without sticking to the mold. Poorly designed ejection systems can lead to defects like scratches, dents, or even cracks in the finished parts, which can diminish product quality and lead to costly rework or waste.
Furthermore, the materials used in constructing mold bases, such as high-grade steel or aluminum, are chosen for their strength, durability, and resistance to wear. This helps the mold base withstand the repeated pressure and heat cycles of the injection process, prolonging its lifespan and ensuring consistent product quality over time. The ability to endure high-stress conditions without degrading or losing precision is crucial for maintaining productivity and minimizing downtime in production lines.
Overall, the quality of a mold base is directly linked to the quality of the finished injection molded products. By providing structural integrity, aiding in thermal management, ensuring smooth ejection, and enduring high operational demands, mold bases serve as a cornerstone of successful injection molding operations. Investing in a high-quality mold base not only improves product outcomes but also enhances operational efficiency and reduces long-term maintenance costs, making it a critical factor in achieving consistent and reliable production.
Chimold mold base uses high-quality materials and precision CNC processing technology to provide high precision of ±2μm to ±5μm and durability of up to 500,000 to 3,000,000 injections. Our customized services and diversified mold standards ensure high efficiency from design to production, and are ideal for precision plastic injection molding in industries such as home appliances, automobiles, electronics and mobile phones. Choosing Chimold means choosing excellent quality and reliable performance.
The mold base is a fundamental component that significantly influences the quality of injection-molded products. Its role in ensuring dimensional accuracy, optimizing thermal management, enhancing surface finish, and facilitating smooth ejection makes it a critical factor in the injection molding process. By carefully designing, selecting materials, and maintaining the mold base, manufacturers can achieve high-quality molded products with consistent performance, even in complex or high-volume production scenarios. The right mold base not only improves product quality but also enhances productivity, reduces defects, and ultimately drives manufacturing success.
https://www.gcmicgroup.com/Optimizing-Injection-Molding-with-High-Performance-Mold-Bases.html
https://www.gcmicgroup.com/Mold-Base
www.gcmicgroup.com
Chimold