Flawless Connections: Navigating the Types of Joint Flanges in Engineering
3 min read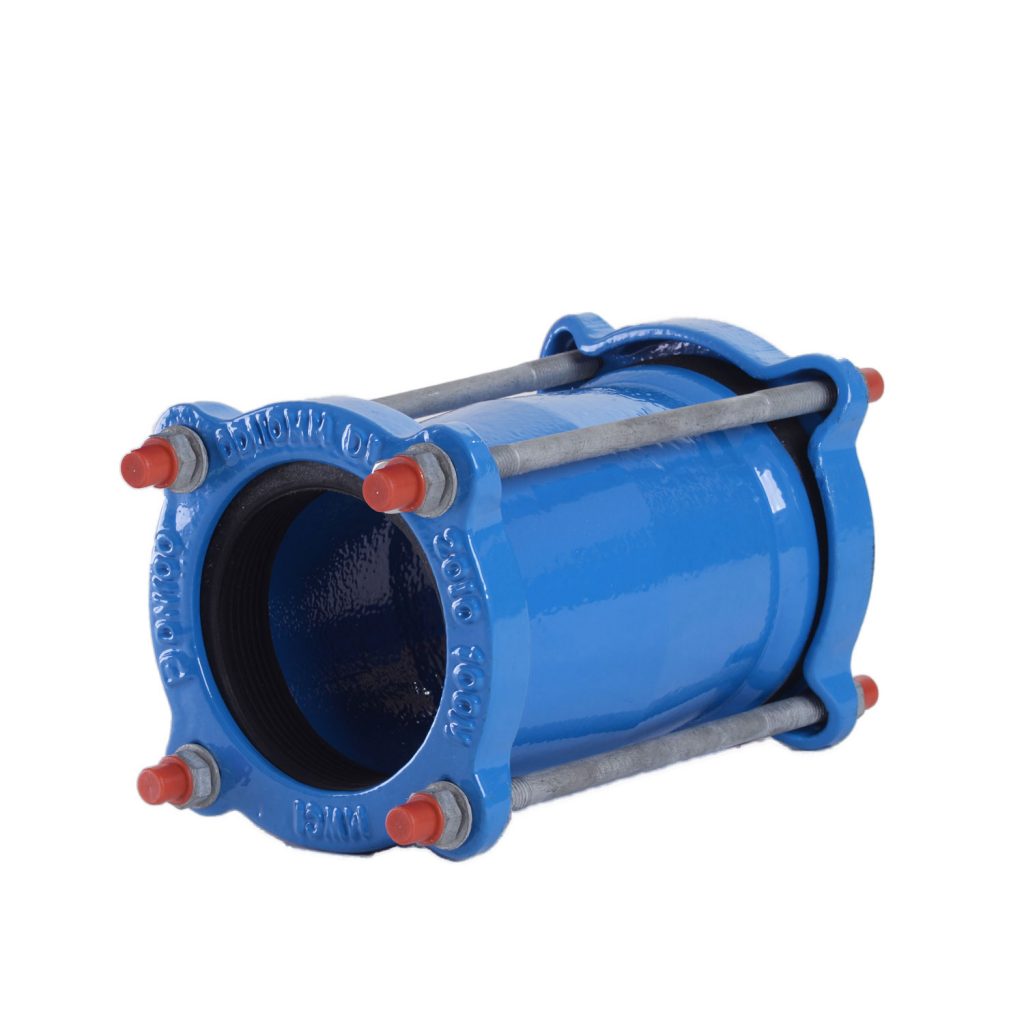
In the intricate world of engineering, joint flanges serve as crucial components, providing a robust and efficient means of connecting pipes, valves, and other equipment. This article delves into the diverse types of joint flanges, offering a comprehensive exploration of their designs, applications, and considerations for optimal performance. Let's unravel the intricacies of joint flanges, essential elements in the seamless flow of fluids and gases within industrial systems.
1. Introduction to Joint Flanges
A. Significance in Piping Systems
Initiate the article by highlighting the paramount role of joint flanges in piping systems. Discuss their primary function of connecting pipes while allowing for easy assembly and disassembly, facilitating maintenance, and ensuring leak-free operation.
B. Types of Joint Flanges Overview
Provide a brief overview of the common types of joint flanges, including weld neck, slip-on, socket weld, lap joint, and blind flanges. Lay the groundwork for a detailed exploration of each flange type.
2. Weld Neck Flanges
A. Design and Application
Examine the design characteristics of weld neck flanges. Discuss their long necks, which provide an extended welding surface, making them suitable for high-pressure and high-temperature applications. Explore how weld neck flanges are prevalent in critical piping systems.
B. Ideal for Rigorous Conditions
Highlight scenarios where the structural integrity and strength of weld neck flanges make them ideal. Discuss their use in applications where severe conditions, such as high pressure or fluctuating temperatures, demand reliable and durable connections.
3. Slip-On Flanges
A. Easy Installation
Dive into the characteristics of slip-on flanges, emphasizing their ease of installation. Discuss how slip-on flanges slide over the pipe and are then welded in place, making them a popular choice for applications where quick assembly is crucial.
B. Cost-Effective Solution
Explore scenarios where slip-on flanges serve as a cost-effective solution. Discuss their simple design, reduced material requirements, and suitability for low-pressure systems, contributing to overall cost efficiency.
4. Socket Weld Flanges
A. Socket Welding Advantages
Examine the features of socket weld flanges, focusing on their socket-like design for pipe insertion. Discuss the advantages of socket welding, including improved flow efficiency and suitability for applications where fluid integrity is paramount.
B. Resistance to Leakage
Highlight how the socket weld design of these flanges contributes to their resistance to leakage. Discuss scenarios where this characteristic is crucial, such as in systems where preventing fluid leakage is of utmost importance.
5. Lap Joint Flanges
A. Unique Design Features
Explore the unique design features of lap joint flanges, including the absence of a raised face. Discuss how they consist of two parts – the stub end and the backing flange – providing flexibility and ease of alignment during installation.
B. Ideal for Piping Systems with Misalignment
Discuss scenarios where lap joint flanges shine, such as in piping systems with potential misalignment. Explore how their design allows for rotational adjustments, making them suitable for applications where perfect alignment is challenging.
6. Blind Flanges
A. Sealing Off Terminations
Examine the purpose and design of blind flanges, which are used to close the end of pipes, valves, or pressure vessel openings. Discuss how blind flanges provide a secure seal, preventing the escape of fluids or gases.
B. Applications in Maintenance and Testing
Highlight the role of blind flanges in maintenance and testing procedures. Discuss their use in isolating sections of a system for repairs, inspections, or pressure testing, contributing to the overall efficiency of industrial operations.
Conclusion: Crafting Precision in Fluid Dynamics
Summarize the article by emphasizing the importance of selecting the right type of joint flange based on the specific requirements of the application. Highlight how a nuanced understanding of each flange type enables engineers to craft precision in fluid dynamics, ensuring optimal performance and reliability in industrial systems.